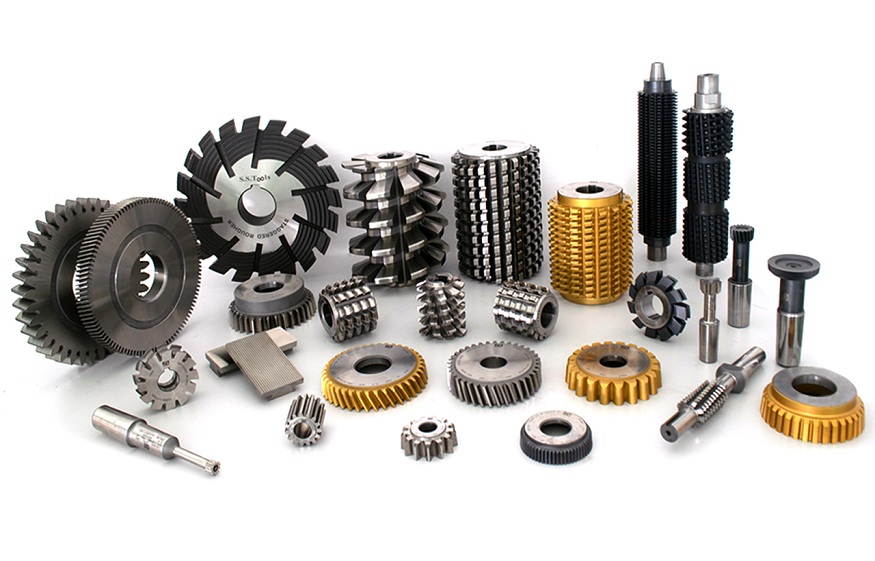
Everything that you need to know about shaping cutters
Many of you might not be interested in knowing more about tools and their mechanism, I was one of those people too until I found out that tools can also be interesting. Let’s have a little insight on what is gear shaping cutter or the different kinds of gear shaping cutters, also let’s understand  how is this entire work is done. Gear shaping is basically a machining process which is made for creating teeth on a gear using a cutter. In simple words you can say that, gear shaping is a convenient and versatile method of gear cutting as it involves continuous, same-plane rotational cutting of gear.
The most common gear-cutting processes that are known to mankind include hobbing, broaching, milling, grinding, and skiving. All of these cutting operations are very common and they may occur either after or instead of forming processes such as forging, extruding, investment casting, or sand casting. I know some of these terms are extremely technical and boring but bare with me, the real process when you get to actually do the work is quite interesting.
The process of setup and equipment’s required are;
The machine that people have been using for the gear shaping process generally consists of components such as a base, a column spindle, and lastly an arbor. In terms of where each of these parts are attached with one another, the gear cutter is mounted right on the spindle, and as for the gear blank, it is mounted on the arbor. The cutter then starts to reciprocate up and down while the work piece is gradually fed into the cutter. At the end of each cutting rotation, the spindle is retracted slightly so as to not cause any more cutting to happen into the new cut teeth of the gear.In the process of gear shaping, a toothed disk cutter is being used. Why you must wonder, it is because it reciprocates in axial rotations. Later on, when the process has started the work piece which is also commonly known as the blank gear rotates on a second shaft called as the spindle. The work piece is then aligned with the cutter and it gradually keeps on feeding right into the cutter while rotating. If by any chance , a two-step process is used then all tooth spaces are partially cut before reaching towards the finished product.
Gear cutters vs. Hobbing.
Gear shaping is known for producing a very high accuracy in surface finishing . Although I don’t think the same is the case with gear hobbing, it is known for giving great movement accuracy. So if we see it from a neutral perspective, both have their own pros and cons depending on what kind of accuracy your gear needs. Judging from the overall opinion of most experts, they seem to say that gear shaping is more accurate than gear hobbing which makes it a better choice but at the same time, based on your demands it may not work for you.